How to Optimize Your Container Tracking Process
Efficient container tracking is key to a successful logistics operation. This blog post outlines best practices for optimizing your container tracking process, ensuring timely deliveries and cost savings.
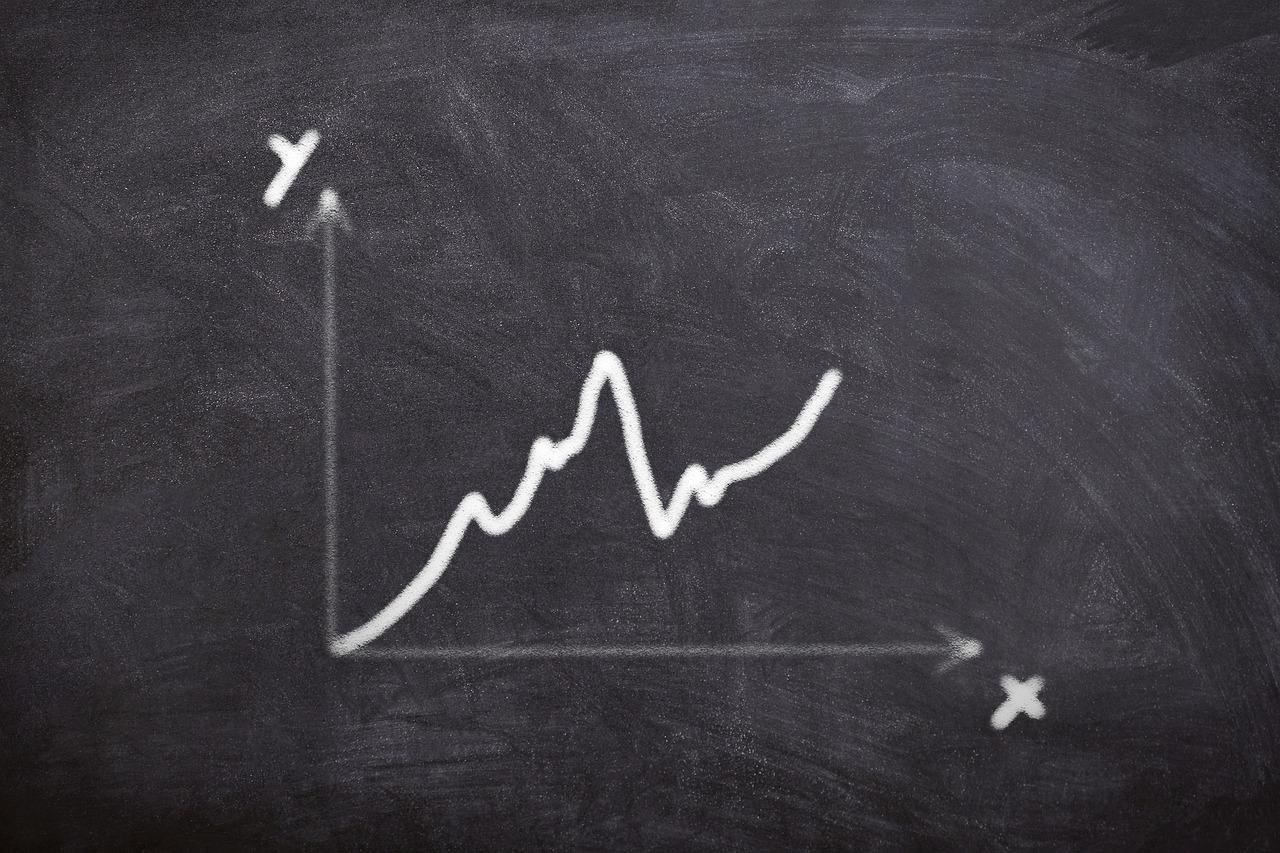
Related Blogs
In the complex world of logistics and supply chain management, understanding key terms and practices is essential to ensuring smooth operations. One such term that plays a crucial role in the shipping process is the "Last Free Day." While it might sound like just another logistical jargon, the Last Free Day is critical to cost management, efficiency, and avoiding unnecessary charges. This blog will delve into what the Last Free Day is, why it matters for your business, and how you can manage it effectively to avoid potential pitfalls.
What is the Last Free Day?
The Last Free Day is the final day that a shipping container can be stored at a port or terminal without incurring additional charges, commonly referred to as demurrage fees. When goods arrive at a port, they are given a certain number of free days for storage. During this time, the importer can arrange for the cargo to be picked up and transported to its final destination. Once the Last Free Day passes, the container begins to accumulate demurrage fees, which can quickly add up and become a significant cost for businesses.
Example: If a container arrives at a port on August 1st and is given five free days, the Last Free Day would be August 5th. From August 6th onwards, demurrage charges would apply if the container has not been picked up.
Why is the Last Free Day Important?
Understanding the Last Free Day is crucial for several reasons, especially when it comes to cost management and operational efficiency.
- Cost Avoidance: Demurrage fees can be expensive. Ports and shipping companies impose these charges to incentivize quick removal of containers, preventing congestion. If a company fails to collect its cargo before the Last Free Day, these fees start to accrue daily, leading to potentially thousands of dollars in additional costs. Knowing and managing the Last Free Day helps businesses avoid these unnecessary expenses.
- Operational Efficiency: The supply chain’s efficiency relies on the timely movement of goods. Delays in picking up containers from ports can cause a ripple effect, leading to late deliveries, dissatisfied customers, and disrupted schedules. Managing the Last Free Day ensures that containers are moved on time, keeping the supply chain running smoothly.
- Port Congestion Management: Ports have limited space and resources. When containers are not picked up on time, it contributes to congestion, making it harder for ports to manage incoming shipments efficiently. This congestion can lead to further delays and complications for all parties involved. Adhering to the Last Free Day helps prevent port congestion, benefiting the entire logistics ecosystem.
- Customer Satisfaction: Customers expect timely delivery of their goods. Delays caused by missed Last Free Days can lead to unhappy customers and damage to a company’s reputation. By managing the Last Free Day effectively, businesses can meet delivery deadlines and maintain high levels of customer satisfaction.
How to Identify Your Last Free Day
Identifying the Last Free Day for your shipment is a straightforward process but requires attention to detail. Here's how you can do it:
- Check Your Shipping Documents: The Last Free Day is usually specified in the shipping documents, such as the Bill of Lading or Arrival Notice. These documents will provide details about the number of free days allowed and the date the container arrived at the port. Calculate the Last Free Day based on these details.
- Contact Your Shipping Line or Port: If the Last Free Day is not explicitly mentioned in your documents, you can contact your shipping line or the port where your cargo is stored. They can provide the exact date when demurrage fees will begin to apply.
- Use Online Port Systems: Many ports offer online systems where you can track your shipments and check the Last Free Day. These systems provide real-time updates and are a convenient way to stay informed about your container’s status.
Factors Affecting the Last Free Day
Several factors can influence the Last Free Day, and understanding them can help you better manage your shipments:
- Port Policies: Different ports have different policies regarding free storage days. Some ports may offer three free days, while others may provide five or more. It's essential to be familiar with the specific policies of the port where your cargo is arriving.
- Shipping Line Agreements: The agreements between shipping lines and ports also play a role in determining the Last Free Day. Some shipping lines may negotiate additional free days as part of their contract with the port. Understanding your shipping line’s agreements can give you more flexibility.
- Customs Clearance: Delays in customs clearance can affect the Last Free Day. If your cargo is held up for customs inspection or requires additional documentation, it can lead to delays in picking up the container. It's essential to ensure all customs paperwork is in order to avoid these delays.
- Public Holidays and Weekends: The Last Free Day may be extended if it falls on a public holiday or weekend when the port is closed or has limited operations. Always check the port’s operating hours and holiday schedules to plan accordingly.
Managing the Last Free Day Effectively
To avoid the complications and costs associated with missing the Last Free Day, businesses should implement strategies to manage this aspect of the shipping process effectively. Here are some practical steps:
- Set Up Alerts and Reminders: Utilize technology to set up alerts and reminders for the Last Free Day. Many logistics software solutions offer features that can notify you as the Last Free Day approaches. These reminders can help you stay on top of deadlines and ensure timely action.
- Coordinate with Transport Providers: Plan and schedule transportation in advance to ensure that trucks or other transport means are available to pick up the containers before the Last Free Day. Building strong relationships with transport providers can help ensure that you have the necessary resources available when needed.
- Monitor Shipments in Real-Time: Use tracking systems to monitor the status of your shipments in real-time. These systems provide visibility into when your containers will arrive at the port and allow you to plan accordingly. By having up-to-date information, you can adjust your plans if there are any changes or delays.
- Prioritize Documentation: Ensure all necessary documentation for customs clearance is complete and accurate before your shipment arrives. Having all paperwork in order can help avoid delays in customs processing, which can, in turn, prevent delays in picking up your containers.
- Maintain Communication with Port Authorities: Establish clear communication channels with port authorities and shipping lines. If there are any issues or delays, being in regular contact can help you find solutions and make arrangements to avoid demurrage charges.
- Conduct Regular Audits: Regularly audit your shipping and logistics processes to identify areas for improvement. Audits can help you identify bottlenecks, inefficiencies, and potential risks, allowing you to implement changes that enhance your ability to manage the Last Free Day.
The Impact of Missing the Last Free Day
Failing to manage the Last Free Day effectively can have significant consequences for your business. Here are some of the potential impacts:
- Increased Costs: Demurrage fees can quickly escalate, leading to substantial additional costs. These fees can eat into your profit margins and affect your bottom line. In some cases, demurrage charges can be so high that they exceed the value of the goods being shipped.
- Delays in Delivery: Missing the Last Free Day can lead to delays in delivering goods to customers. These delays can disrupt supply chains, affect production schedules, and lead to stockouts, impacting your ability to meet customer demand.
- Reputation Damage: Consistently missing delivery deadlines and incurring demurrage charges can damage your business's reputation. Customers may view your company as unreliable, leading to lost business and negative reviews.
- Legal and Contractual Issues: Some contracts with customers or suppliers may include clauses related to delivery timelines. Missing the Last Free Day and subsequent delivery delays could lead to contractual breaches, legal disputes, and potential penalties.
Real-World Example: The Cost of Missing the Last Free Day
Consider a scenario where a company imports electronics from Asia to a port in the United States. The company is given five free days to pick up the containers after arrival. Due to miscommunication and poor planning, the company misses the Last Free Day and fails to pick up the containers for an additional ten days. The port charges $100 per container per day in demurrage fees.
If the company has ten containers, the demurrage charges would amount to:
10 containers x 10 days x $100 = $10,000
In this example, the company incurs $10,000 in additional costs due to missing the Last Free Day. These charges could have been avoided with better planning, communication, and management of the Last Free Day.
Conclusion
Understanding the Last Free Day is essential for any business involved in importing goods. It plays a crucial role in cost management, operational efficiency, and customer satisfaction. By effectively managing the Last Free Day, businesses can avoid unnecessary demurrage fees, ensure timely delivery of goods, and maintain a positive reputation in the industry.
To manage the Last Free Day effectively, businesses should invest in technology for tracking and monitoring shipments, set up alerts and reminders, coordinate with transport providers, prioritize documentation, and maintain clear communication with port authorities. Implementing these strategies will help businesses stay ahead of deadlines, avoid costly mistakes, and keep their supply chains running smoothly.
In conclusion, the Last Free Day is not just a date on a calendar; it is a critical aspect of logistics management that can significantly impact a business’s success. By understanding and managing the Last Free Day, businesses can maximize efficiency, reduce costs, and ensure that their goods reach customers on time.
Get In Touch
We’re here to support you. Fill out our contact form, and we’ll get back to you promptly.
Email Us
Prefer to write? Send us an email with your questions or comments, and we will get back to you as soon as possible.
support@lastfreedaylook.com
Full Name
Email Address
Phone Number
Message